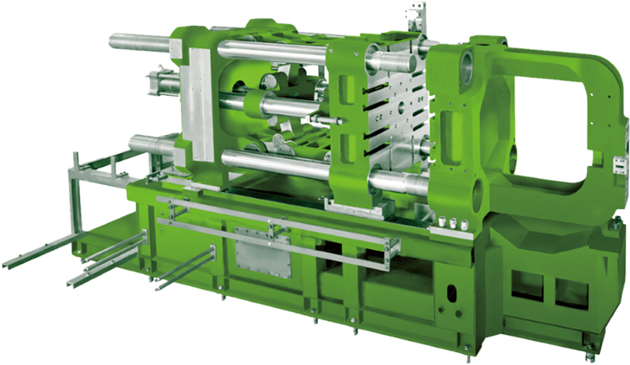
A Guide About Die Casting and Its Types
2022 / 05 / 04
Die casting involves injecting molten metal that has low melting points like aluminum and zinc into the mold for the die casting machine and then allowing it cool. Based on the melting point, it can be done using two different processes (hot as well as cold chamber casting) and can be used to create easy and complicated sheet metal components.
What is Die Casting?
Die casting refers to a method that involves melting the metals with low melting points and injecting them into a created mold, also known as a Die casting mold. A mold or tool is made from steel fabricated to be used in a single task using manufacturing processes like CNC cutting. Therefore, sheet metal components made by die-casting are of the highest precision, accuracy, and repeatability used for the auto extractor
Die Casting Types
The two most common kinds of casting equipment include Cold chamber and Hot chamber machines. The variations of these two major casting processes are squeeze, vacuum low-pressure, and semi-solid casting. Different casting methods for die casting are selected over others based on the material used, its dimension, geometry, and complexity.
The Hot Chamber Process
The hot chamber procedure is also known as the gooseneck or hot die casting procedure. In this method, the plunger and chamber of an injection mechanism are immersed into the molten bath of a furnace made of metal. They are used for low melting point metals that aren't chemically damaging the dipped assembly. After the dies are shut, the plunger is pulled back and opens the chamber's port to allow the hot metal to flow. The plunger then seals off the port and pushes the molten metal through the die cavity via the gooseneck as well as the nozzle.
Cold Chamber Process
When using the cold chamber procedure, the molten metal is put into the shot sleeve or chamber component of an injection cylinder before pressing into the mold. Since the sleeve isn't heated, this process is called the cold chamber procedure. Since the metal melting pan is distinct, it does not suffer from corrosion.
The cold chamber process begins when the molten material is moved to the shot chamber via the furnace via the hole for pouring. A hydraulic plunger closes the port of the cold chamber and pushes the metal into the cavity under pressure through the auto sprayer. The pressure can range from 30Mpa to 150 MPa.
Vacuum Die Casting
The process of vacuum die-casting is an additional option to traditional die-casting techniques and is typically related to a cold-room process. A vacuum source eliminates the gas and air that are trapped in the die cavity before the metal molten enters the chamber. This kind of aluminium casting machine reduces the chance of turbulence and gas inclusions and is helpful for applications that are intended for after-cast heating treatment.
The Process Of Squeeze Casting
Components for cars and mortars may be made using a process called "squeeze casting," which combines the processes of "liquid metal forging" and "casting." It is a sequence of operations in the squeeze-casting procedure. The molten metal is squeezed into the mold while filling in the recessed areas of the mold, which produces exceptionally dense products after the process. This technique is also employed to produce reinforced matrix composites made of metal that are made when the molten aluminum enters into a strengthening structure.
Conclusion
Die casting is extensively used across all industries, particularly in the automotive industry. Different kinds of die casting are used to accomplish this. The guide above provides all the information on the various types of castings that are used in industries.